SHEPHERD’s delight – a new resource for explosion exceedance
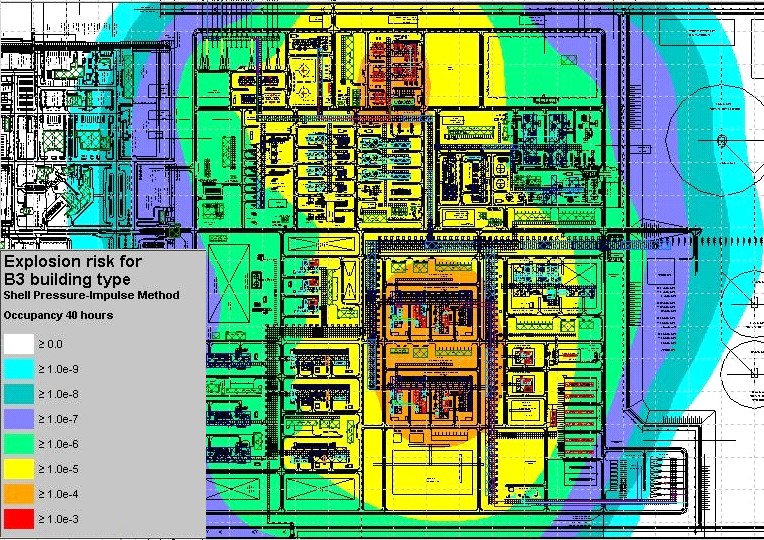
There are about 2 major explosions around the world every year in the refinery and petrochemical industry. The effects can be devastating, causing fatalities and significant economic losses. Often the fatalities and many of the serious injuries occur inside buildings on the site.
At any particular refinery unit, the likelihood of a major explosion is about 1 in 2,000 years [Ref. 1]. The explosion risk to people inside plant buildings will depend upon the type of building construction, the location, the plant processes and materials. A quantitative analysis can establish where risk is intolerably high and risk reduction options are appropriate (see Table 1).
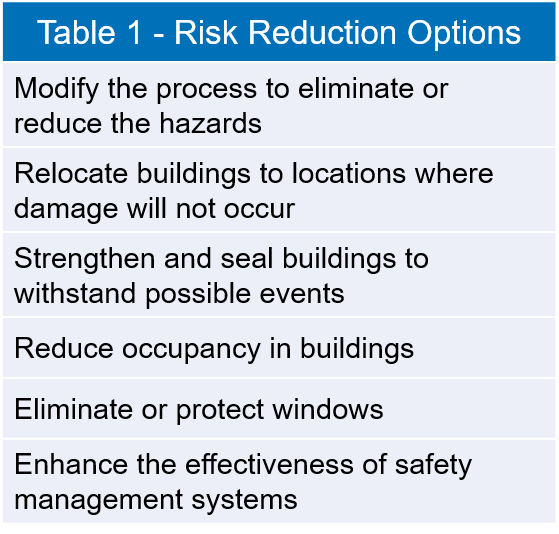
These options may involve major cost or feasibility constraints and would require analysis to determine the most effective approach. This type of analysis is called an “explosion exceedance study” and calculates the frequency and distribution of all foreseeable explosion overpressures and impulses over the area of the plant.
FIT-FOR-PURPOSE EXPLOSION ANALYSIS
A full study can be an expensive exercise. It involves starting with a single scenario – a flammable release – and working through its consequences and frequency. A hierarchy of analytical tools, ranging from simple screening tools to full state-of- the-art computation, could be applied at each step. Then, the analyst returns to the start and works through the next scenario, finally summing all foreseeable risk contributions to personnel in occupied buildings.
A simpler, but more pragmatic, version of this exceedance methodology has been developed by Shell Global Solutions and implemented in a suite of software risk tools known as “SHEPHERD”. The result is a fully probabilistic tool that has been extensively validated by experiment and by comparison with historical data. Significant effort has been applied to minimise loss of accuracy while increasing speed.
GENERIC CURVES
At the heart of SHEPHERD lie generic data curves. They reduce the amount of explosion modelling that would otherwise need to be done and also eliminate the need for structural response analysis for buildings [Ref. 2]. The curves include:
1. A distribution of source overpressures based on Shell’s detailed studies and research. This allows source overpressure, for various volumes of flammable gas in a particular area, to be derived from a simple correlation rather than by explicit case-by-case explosion modelling.
2. Three models for the vulnerability of occupants to building damage, including the API RP752 model and two models based on research of generic building types.
This approach greatly simplifies the analysis, enabling studies of large facilities to be done much faster (see Table 2).
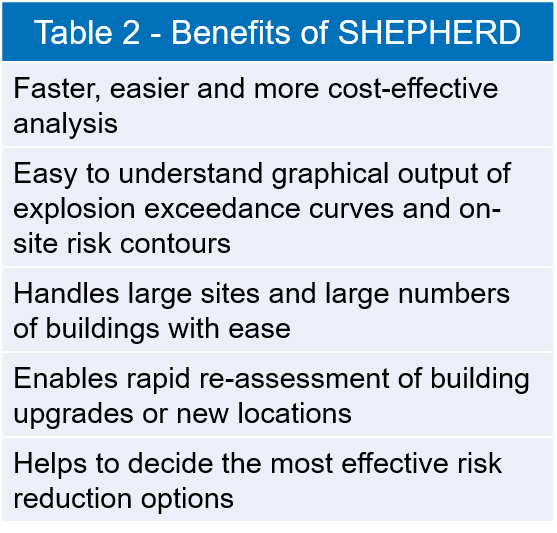
CONCLUSION
The accidental release and ignition of flammable vapours or runaway reactions in refineries and petrochemical plants present major potential explosion hazards to plant personnel and plant assets. Quantitatively analysing the risk of fatality enables sensible decisions regarding risk reduction measures, but traditionally this can be time consuming and expensive.
The new SHEPHERD methodology and software provides a quick, cost-effective and validated approach which is especially suited to supporting early assessment of large sites with high numbers of buildings. Note finally that a full assessment can still be warranted when making critical decisions, such as ones that involve extreme consequences with borderline risks.
References
1. API RP752, Management of Hazards Associated with Locations of Process Plant Buildings, May 1995.
2. Explosion Exceedance According to API RP752 and SHEPHERD, G.A. Chamberlain, Shell Global Solutions, IChemE Hazards XIX, Manchester, March 2006.
This article first appeared in RISKworld Issue 9.