Winning hearts and minds
Over the years there has been substantial progress in reducing health, safety and environmental (HSE) risks (Figure 1). Initially, significant benefit came from improving the intrinsic safety of engineering. As the scope for further enhancement reduced, attention was drawn to improving management systems. Now HSE specialists are looking to deliver improvements through positive changes in organisational culture and personal behaviour.
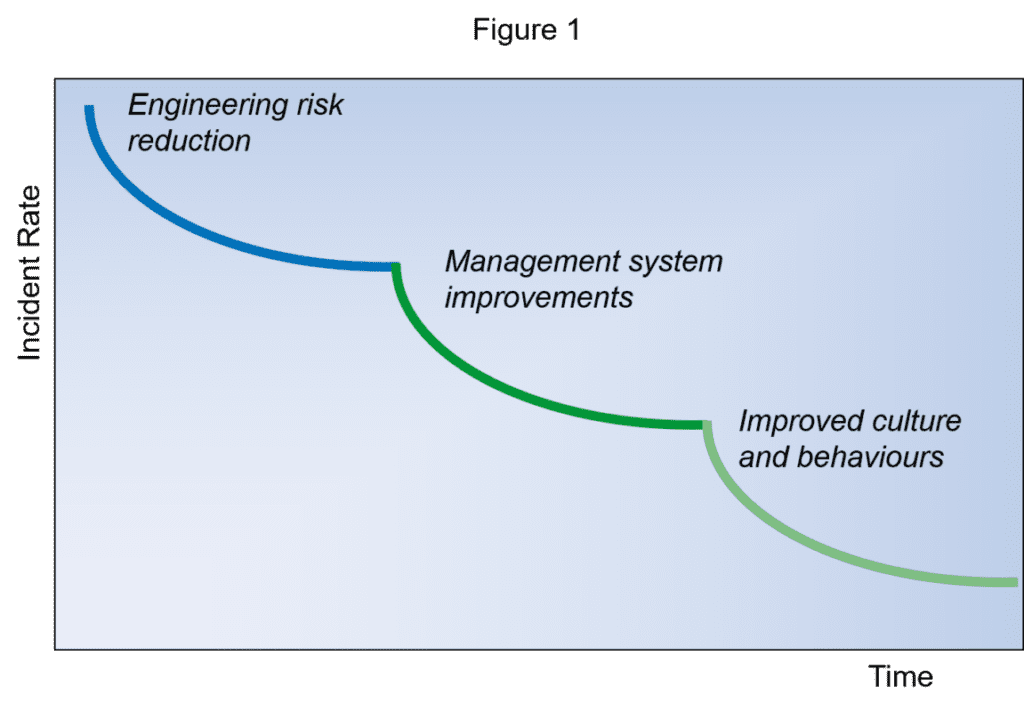
COMPANY CULTURE
Safety in the workplace cannot be managed by focusing on regulations and procedures alone. Ultimately, safety is the result of motivated and competent people working in an organised business, looking after themselves and others. So how does an organisation create an HSE culture where people conduct business safely without having to control their every action?
In 1986 Shell started sponsoring a research programme involving the universities of Leiden, Manchester and Aberdeen (Ref. 1) to better understand what can be done to prevent accidents. In the first instance a culture “ladder” was developed to characterise increasing levels of cultural maturity (Figure 2).
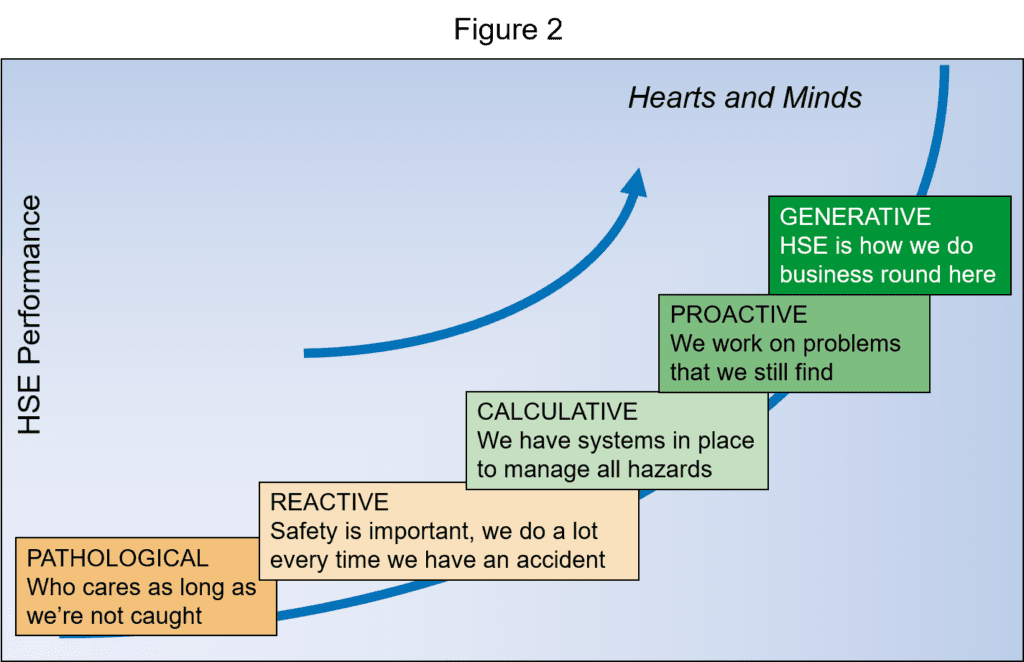
At the lowest level is the Pathological culture where nobody cares as long as they are not caught. At the highest level, the Generative culture, HSE is part of everything that is being done. In between are intermediate stages. Different sets of personal behaviours align with these cultural stages and can be used as “seeds” for people to develop their own personal perspective on preferred behaviours.
HEARTS AND MINDS
Research has shown that a highly motivated workforce, from the management team to those on the shop floor, can be equated with a highly developed HSE culture. These findings have been translated into “Hearts and Minds” tools that aim to get everyone to understand and agree on the value of positive HSE behaviour and foster a desire for outstanding performance.
The tools are “light”, self-contained, and designed for non-expert people, with the background science built in. They are tailored for small syndicate groups, taking no more than a few hours to identify and solve a problem. They help to understand your HSE culture, manage rule breaking and improve supervisory skills.
TRIPOD
The research also led to the Tripod methodology, recognised today as a leading tool for human and organisational factors evaluation (Refs. 2, 3).
Tripod Delta is a diagnostic tool that helps to determine the susceptibility of an organisation to possible incidents. The tool uses a technique that resembles psychometric testing, where a survey of all employees builds an objective picture of the strengths and weaknesses of the organisation within the framework of 11 “basic risk factors”. The results can be used to initiate pro-active and sustainable strategies for reducing and managing risk.
Tripod Beta is a reactive tool facilitating the investigation and analysis of incidents in order to prevent recurrence. The strength of the method lies in the identification of latent or hidden failures within the organisation that contributed to the incident, instead of focusing on the immediate causes, to enable lasting and sustainable improvements.
TRIPOD – DOES IT WORK?
- 30% fewer accidents in 6 months, following use of Tripod Delta at four drilling rigs working for NAM in the Netherlands.
- 25% cost of a traditional audit
Sources: Ref. 4 and 5
CONCLUSION
The approaches outlined represent an alternative to the “command and control” attitude prevalent in many companies. Winning the hearts and minds requires the creation of a culture in which safe behaviour is considered more important than mere compliance.
References
1 – van der Graaf, Hudson, SPE Conference Kuala Lumpur 2002, paper 73941
2 – Germanischer Lloyd, funded by EC, Deliverable D1, 1999
3 – Technical Research Centre of Finland, 2000
4 – Watts, 1999, Proceedings of First International Tripod Symposium
5 – Pearce, Tripod in Shell Expro, 1996 and 1997
This article first appeared in RISKworld Issue 4.