Ten good practices for developing HSE cases in the oil industry
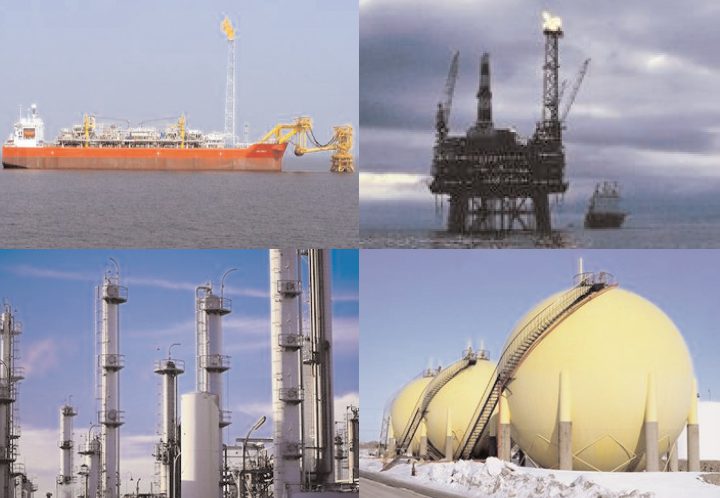
The requirement to develop a formal safety case for any major oil and gas facility has been in place for many years in regulated environments such as the UK and Australia. Today, oil companies and industry associations are applying this requirement in other regions of the world where such legislation does not currently exist. This provides an opportunity to learn from experience and develop concise and pragmatic health, safety and environment (HSE) cases.
Well developed HSE cases not only protect lives and the environment, but help a business manage its assets, maintain its competency and reduce the risk of lost production.
1. USE WHAT YOU’VE GOT, WORK OUT WHAT YOU’RE MISSING
All facilities will have at least some, and probably many, existing HSE studies. There is no need to re-do everything from scratch. A useful approach is to conduct a ‘gap analysis’ of these studies against a set of requirements, e.g. an international or industry standard, to identify what is missing or inadequate.
2. QUALITATIVE RISK APPROACHES CAN IDENTIFY MOST IMPROVEMENTS
There is no need to rush into time consuming, full quantification of HSE risks. Experience based, qualitative risk assessment can often identify the vast majority of possible risk reduction improvements.
3. RECORD ALL HSE RISKS, THAT MAY NOTHING IS OVERLOOKED
Identifying and assessing all health effects, environmental impacts, workplace safety hazards and major accident events provides an all-encompassing approach. Using a ‘risk register’ to document these risks creates a valuable reference guide for the facility. Having separate, but inter-linked, registers for health, safety and environment risks can be even better – it improves understanding of the subtleties in how they are managed.
4. BUT DON’T NEGLECT MAJOR ACCIDENT EVENTS
While some workplace tasks such as grit blasting can be risky for an individual, they usually rely on the competency of the individual supported by robust procedures to assess and control the risk. It is only major accident events such as loss of hydrocarbon containment that have the potential for massive fatalities, environmental impact, economic loss and reputation damage. They warrant detailed and thorough analysis, followed by an appropriate level of verification.
5. QUANTIFYING RISK LEVELS DOES HELP IN SOME SITUATIONS
The purpose of quantitative risk assessment (QRA) is to help reduce risk by supporting risk-based decision-making. It is especially powerful when applied with cost-benefit analysis to compare options during the design phase or modifications during operations. But estimating absolute risk levels solely for comparison with quantitative criteria can be open to manipulation of data, methods and assumptions.
6. THERE IS NO EASY FORMULA FOR DEMONSTRATING RISK IS ALARP
The ALARP level is reached when the time, trouble and cost of further risk reduction becomes unreasonably disproportionate to the benefit gained. This implies a mathematical formula but in practice it amounts to taking a balanced view and reaching a defensible consensus on prioritised improvements. A convincing ALARP demonstration lies in the documented consideration of improvement options, both implemented and discounted, at a level of resolution appropriate to the facility life-cycle and magnitude of risk.
7. INVOLVE PEOPLE, THEY KNOW WHAT’S REALLY GOING ON
Involving personnel in developing the HSE case is critical in gaining ownership of HSE risk management. Commissioning a consultancy to arrive, collect information and then leave to produce a report from their office is a recipe for inaction. Opportunities to involve personnel include participating in workshops, highlighting where safety systems or procedures do not have the benefits claimed, commenting on the accuracy of technical reports, and participating in training. A major benefit of the case comes from the process of preparing it, rather than the document itself.
8. DON’T JUST ANALYSE RISK, UNDERSTAND HOW IT IS MANAGED
One of the most potent and increasingly popular risk assessment techniques is the ‘bow-tie’ method because it highlights the crucial link between risk controls (whether hardware or procedural) and the management system and personnel competencies necessary for their ongoing effectiveness. It thus helps to ensure that risks are truly managed by competent people, rather than just analysed.
9. LIVE BY THE HSE CASE, DON’T STICK IT ON THE SHELF
It is only through the continued communication and implementation of the HSE case that sustainable improvements in HSE are likely to be maintained. Examples of deliverables in a roll-out plan include information presentations, leaflets, booklets, e-learning packages, accountability packs and intranet websites.
10. AND FINALLY, RISK MANAGEMENT REQUIRES ACTION NOT WORDS
It is surprising how many people need reminding that risk levels will remain the same, or even increase, until real improvements are fully implemented. A case can generate a large number of recommendations and these need to be properly managed. More analysis or rousing speeches are not the solution. The solution is more action.
This article first appeared in RISKworld Issue 10.