EMIT Optimisation – Getting more out of existing equipment for less
A key challenge facing operators is to optimise their preventive maintenance regimes such that the safety of the plant is maintained, the availability of the plant is maximised and disruptive corrective maintenance or replacement of equipment is minimised.
Traditional preventive maintenance is often initially prescribed by original equipment manufacturers on the basis of generic operating cycles, rather than adjusted for operator specific usage, system location or online condition monitoring.
The Examination, Maintenance, Inspection and Testing (EMIT) optimisation process seeks to understand the plant or system function, highlight the significant equipment items, review the current EMIT regime and reduce the associated workload while maintaining plant safety and improving plant availability.
WHY CONDUCT AN EMIT OPTIMISATION STUDY
The total cost of maintenance is the sum of the cost of preventive and corrective maintenance. The optimal maintenance zone is where these two costs are balanced, as illustrated in Figure 1. Locating this balance is an age old problem and this is where an EMIT optimisation study helps. The study aims to establish a cost and plant availability benchmark for the existing maintenance regime, by combining data from current maintenance planning with operating and replacement/repair costs, and then proposing improvements to the maintenance regime to reduce the maintenance burden and improve availability.
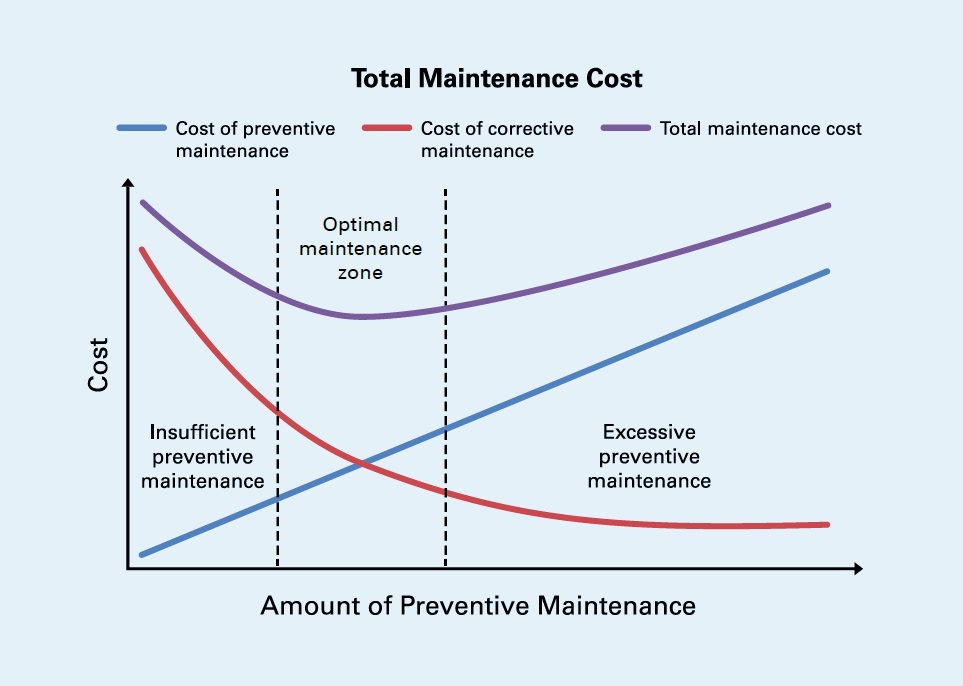
Ideally, the EMIT optimisation process should be embedded within the design phases of projects, where maintenance and access requirements can be considered along with the other system requirements; however it is also very effective at any stage of a system lifecycle.
HOW IS EMIT OPTIMISATION UNDERTAKEN?
The EMIT optimisation process can be broken down into five stages:
- Identify critical plant
Identify plant items that critically affect the safety function or availability of the plant, through lack of redundancy for instance. All other components can potentially be considered as ‘run to failure’ items, although this may be influenced by other factors. - Understand the failure modes and effects
Conduct a Failure Modes and Effects Analysis (FMEA) or an equivalent means of identifying failure mechanisms, and consequential effects. - Evaluate existing maintenance
Review the existing maintenance regime (or the proposed regime if new plant is being considered) to establish:
- Difficulty (specialist equipment, training, etc.)
- Location of plant (access arrangements, confined space issues, etc.)
- Downtime (periodicity, maintenance workload, preparation time, etc.)
- Operating experience (condition of plant, maintenance observations, failures, etc.)
- Associated risk (impact on adjacent plant, exposure of personnel, etc.)
- Apply predictive maintenance techniques
Consider applying predictive maintenance techniques such as corrosion, thermography and vibration analysis, taking into account the associated implications, including costs and manpower. - Recommended changes to the maintenance regime
On the basis of the findings and industry best practice, recommendations can be made to adjust the current maintenance regime toward an optimised state.
TOO FAR TOO FAST?
The conclusions of any EMIT optimisation study are influenced by uncertainties in data and assumptions used. A staged approach to recommended reductions in proactive maintenance should therefore be taken to guard against a spike in failures and reactive maintenance costs which would ultimately negate any realised benefits. Further reductions in maintenance burden can be delivered in subsequent iterations where supported by operational experience or condition monitoring trends.
CONCLUSION
The EMIT optimisation process can better balance the plant maintenance burden by focusing resources on critical plant to achieve safety and availability goals in a continuous and proactive manner.
This article first appeared in RISKworld issue 31