The human factor – cost-effective safety critical task analysis
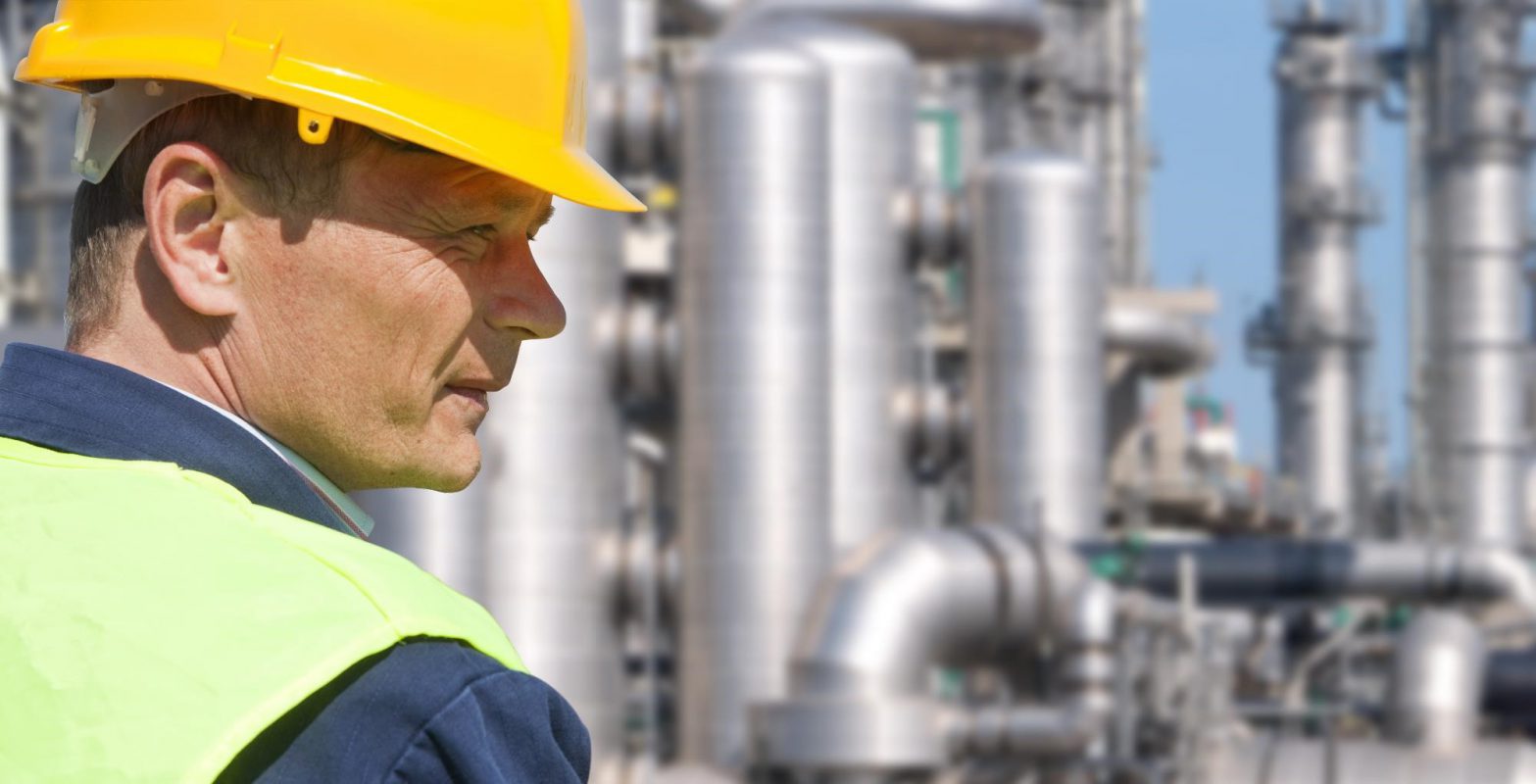
Human failures have contributed to many major accidents in high hazard sectors, such as Chernobyl, Ladbroke Grove and Deepwater Horizon. However, the analysis of safety critical tasks has lagged behind efforts to analyse hardware failures, mainly driven by the perception that assessing the enormous number of tasks at an industrial facility would be too time consuming. Today, practical methods have been developed to help the cost-effective analysis of safety critical tasks.
WHAT IS SAFETY CRITICAL TASK ANALYSIS?
Task analysis is the process of breaking down a task into its component subtasks and determining a plan for how the subtasks should be carried out.
Safety Critical Task Analysis (SCTA) focuses on those tasks which are safety critical, to make sure that they are undertaken correctly, when required. SCTA determines the potential for human failures when conducting critical tasks and identifies the current and potentially additional controls required to prevent or mitigate such failures.
WHAT ARE THE DIFFICULTIES AND CHALLENGES WHEN CONDUCTING SCTA?
Accurate and effective SCTA requires key information about how the tasks are carried out in reality. One way to collect information for SCTA is to run workshops with the teams who perform the actual tasks. However, experience has shown that this approach can be very resource intensive, time consuming and inefficient. Further, and particularly for smaller and leaner organisations, the experienced workers who possess the required knowledge may not be available to participate in lengthy workshops. Therefore, a compromise must be reached between collecting sufficient, accurate information for SCTA and minimising cost, time and resources.
A PRACTICAL APPROACH TO SCTA
A practical four-step approach to SCTA is outlined below. This complies with guidance from the Energy Institute (Ref. 1), but adopts time- and cost-saving strategies such as constraining scope, applying checklists, making full use of existing written material and interviewing or observing appropriate personnel.
Step 1 – Identify safety critical activities
Safety critical activities are those activities which have a causal relationship with major accidents. The first step establishes what major assessment.
For a facility of a specific type (e.g. drilling rig, onshore refinery), a list of typical operating and maintenance activities can be cross-checked against the major accidents to determine which activities are safety critical. Where a facility has a good set of written procedures, these provide a completeness review, but application of a standard activity list saves time and ensures the analysis is pitched at the right level from the start.
Step 2 – Prioritise safety critical activities
Inevitably, a facility will have many safety critical activities and detailed analysis of them all would take considerable time and effort. Initially therefore, the analysis should focus on the most safety critical of activities, which can be prioritised according to their significance for major accidents. For example, activities which directly cause a major accident may be deemed more critical than activities that mitigate the consequences of a major accident. Additionally, if there is a clear link between the activity and previous incidents or near misses then the activity may also be prioritised.
Traditionally, Steps 1 and 2 of the process are undertaken in a multidisciplinary workshop but a relatively accurate first pass can be achieved by review of the safety case, incident records, etc. Workforce involvement is crucial, however, and the prioritised list of activities must be reviewed and agreed with those who are familiar with operations before proceeding to Step 3.
Step 3 – Represent safety critical subtasks
Starting with the most critical activities, the aim of this step is to establish a step-by-step description of the subtasks involved, ready for further analysis. This may be achieved by reviewing written procedures or task instructions, interviewing workers, or by observing the activity directly or via ‘walk-through’. A combination of all three is recommended, but the most effective approach depends, for example, on the quality of the procedures, availability of personnel for interview, etc.
Step 4 – Safety critical task analysis
Again, it is important to focus effort on the task steps which are most critical. The potential consequences of a human failure in carrying out the task step determine the criticality, as does the level of human involvement. Further analysis is then only carried out for those subtasks which fall into the high priority zone of a pre-defined task criticality matrix.
For each of the subtasks identified as high priority, potential human failures are identified by applying a standard checklist. Then the possible consequences of the failure are described – if major accident level consequences are not possible, further analysis of the subtask is not required. Person-, job- and environment specific Performance Influencing Factors (PIFs) which may encourage human failure are recorded using a standard checklist of factors to ensure efficiency and completeness. Experience shows that PIFs are best gathered through interviews and observations to explore any genuine human factor-related concerns.
There may already be control measures in place to prevent failure of a subtask, or to mitigate the consequences if a failure occurs. Suggested additional controls should also be sought and may include improvements in procedures, engineering modifications, improved access to equipment and provision of training or additional checks. Where additional controls are suggested, above and beyond mandatory controls required by law and established good practice, their benefit, in terms of risk reduction, and the effort involved in implementing them, need to be considered in order to decide if implementation is warranted on the grounds of reasonable practicability.
Where there are limits on workshop time and resources, Steps 3 and 4 are essentially completed through a combination of documentation review, interview and task observation. However, a concluding workshop to review findings and endorse actions is an essential final part of the SCTA process.
CASE STUDY
For a modestly sized offshore platform (10 producing wells, single processing train), about 40 Safety Critical Tasks (SCTs) were identified, for example:
- Control room operations
- Process train pressurisation
- Sphering (pigging)
- Well start-up
The initial screening to identify the SCTs took 4 days plus a 1 day workshop and a further day for post-workshop analysis.
Three high priority SCTs were analysed in detail, each taking about 4 days onshore and 1 day offshore. Several risk reduction measures were recommended, for example:
- Introduce additional check step into procedure
- Include equipment items as a specific job plan in maintenance management system
- Install ‘hop-up’ or similar to allow access without standing on pipework
- Improve valve labelling
- Install interlock to prevent task from proceeding if safety system is not engaged
- Relocate gauge to allow easier reading
CONCLUSION
SCTA determines the potential for human failures when conducting critical tasks and identifies current and additional controls required to prevent or mitigate such failures and reduce human error-related risks to as low as reasonably practicable levels.
Traditionally, SCTA is carried out in large workshops, which are resource intensive and can be impractical. However, a proven, pragmatic approach is available that complies with recognised SCTA guidance and results in realistic, meaningful risk reduction improvements.
References
1. Guidance on human factors safety critical task analysis, Energy Institute, March 2011 (update due in 2019)
This article first appeared in RISKworld Issue 19