SPV Management – Simple, but brilliant!
Managing Single Point Vulnerabilities (SPVs) within industrial systems can improve safety, reduce unplanned losses, aid maintenance optimisation and rationalise spares holdings. So what are the main steps needed to establish a SPV management system and realise these benefits?
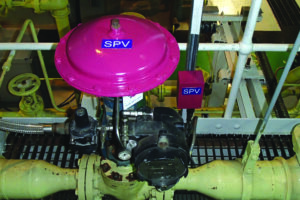
Equipment reliability plays a crucial role in supporting the safe and profitable operation of industrial plant. Introduction of a management system for SPVs is a simple but effective way of controlling critical components and reducing unplanned losses. But, how many plant operators have a strong understanding of their SPVs?
Whilst there have been notable exceptions – the Boeing 737 MAX aircraft crashes in 2018 and 2019 being two recent examples – safety-related SPVs do not normally exist in highly regulated industries because formal safety cases need to satisfy the ‘single failure criterion’. This requires that no single component failure is able to render the safety function of a system unavailable. As a result, the management of SPVs usually focuses on avoiding component failures that adversely affect the availability of a facility.
DEFINING A SPV
The concept of SPVs has been used within the US nuclear power generation industry for many years, where an SPV is defined as:
“A single component whose failure will lead to an immediate automatic or manual trip of the reactor or turbine.”
However, SPVs are not unique to the nuclear industry and their effective management is beneficial to any plant operation where unplanned losses can have a significant business impact.
The first step in the SPV management process is therefore to create an SPV criterion applicable to the specific plant, for example:
“Any single component failure which will result in a loss of production for more than 4 hours.”
IDENTIFYING ALL SPVS
Once the definition of an SPV has been established for the specific plant, the process of identifying SPVs can begin.
This process will vary, depending on the complexity of the plant, but is likely to include:
- Review of previous loss events
- Review of the plant maintenance history
- Plant walkdown and discussions with maintenance and operations personnel
- Assessment of operational experience at similar plants
- Review of plant drawings and manuals
- Studies such as failure modes and effects analysis or reliability block diagram assessment
The exercise allows those critical components within a system that meet the defined SPV criterion to be identified and recorded. The number of SPVs identified will vary greatly, depending on the SPV definition and the complexity of the plant.
REDUCING RISK
With all SPVs known, opportunities to reduce the associated risk can be investigated. Elimination of an SPV is the most desirable approach because it completely removes the potential for an unplanned loss. It could be achieved, for example, by installation of a second pump or valve, but it is not always possible or practicable, given layout or cost constraints. In these cases, appropriate mitigation can be put in place to reduce the SPV risk to an acceptable level.
Potential mitigation measures include strategies such as labelling, condition monitoring, maintenance planning and spares optimisation.
Labelling
SPVs can be flagged within the computerised maintenance management system and the equipment physically highlighted on the plant. Such measures help ensure additional care is taken when planning and working on or around an SPV component (also known as a critical component).
One real-life example of successful labelling comes from the UK nuclear industry, where Risktec has been working closely with EDF Energy. To highlight the importance of critical components to all personnel, regardless of their role, EDF Energy has painted them pink (see Figure 1).
This simple and low cost action creates a dramatic visual impact, turning a paper exercise into something which all personnel can easily understand. Immediately, as you enter a plant area, any critical components stand out and everyone is reminded of their importance.
Condition monitoring
Another mitigation measure is the use of condition monitoring techniques. In particular, non-invasive techniques, such as thermal imaging and vibration monitoring, provide early warning of incipient component failure and allow for the optimum planning of corrective maintenance.
Maintenance planning
It is essential that an adequate maintenance plan is in place for all critical components. This plan may include activities such as:
- Assessing physical condition by routine plant walkdowns
- Reviewing condition monitoring data
- Identifying ageing and obsolescence factors and timescales
- Confirming all associated drawings and manuals are up to date and correct
- Evaluating records of previous maintenance
- Ensuring the most appropriate maintenance techniques are utilised
- Verifying that maintenance workers are suitably qualified and experienced
- Requiring that all components used during maintenance are correctly specified and of high quality
- Allowing adequate time for completion of maintenance
It is crucial that the overall plant maintenance strategy finds the right balance between the maintenance of critical and non-critical components. By identifying critical components, the SPV management process supports maintenance optimisation and the efficient use of resources.
Spares optimisation
Identifying the timeframe of ageing critical components, together with any obsolescence issues, allows for optimisation of spares holding, which can limit the impact of an unplanned loss. Reviewing maintenance activities with the maintainers can further help to optimise the spares strategy. This can reduce the cost of spares by only holding sufficient inventory to allow a rapid return to service should an unplanned loss event occur owing to a single failure.
MONITORING THE MITIGATION MEASURES
A great way of visualising the mitigation barriers in place for each SPV is through bowtie analysis. The bowtie diagram shows the mitigation barriers for each possible cause of failure of the SPV, as well as the current effectiveness of those barriers (see Figure 2).
REVIEW
Having established an SPV management system, it is vital that it is reviewed on a regular basis to ensure that it remains fit for purpose, especially in light of any recent plant modifications. Based on the bowtie diagram, actions can be taken to ensure the mitigation barriers continue to meet the required level of effectiveness. This will include activities such as regular plant walkdowns, review and update of maintenance plans and analysis of any single failures (or near misses) that meet the defined SPV criterion.
CONCLUSION
Whilst SPVs are a simple concept, do operators really know each SPV at their plant and have a clear understanding of the impact of their failure?
Implementing a simple process for the management of SPVs can reduce unplanned losses, improve safety and optimise maintenance activities and spares holding.
The cost savings from reducing unplanned losses alone aresignificant. Can you really afford not to implement an SPV management system?
This article first appeared in RISKworld 41, issued April 2022.
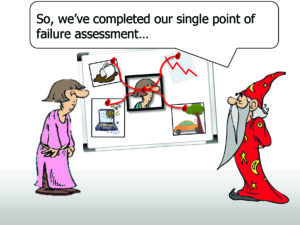